TPM & OEE
TPM & OEE
Driving Value from Asset Maintenance
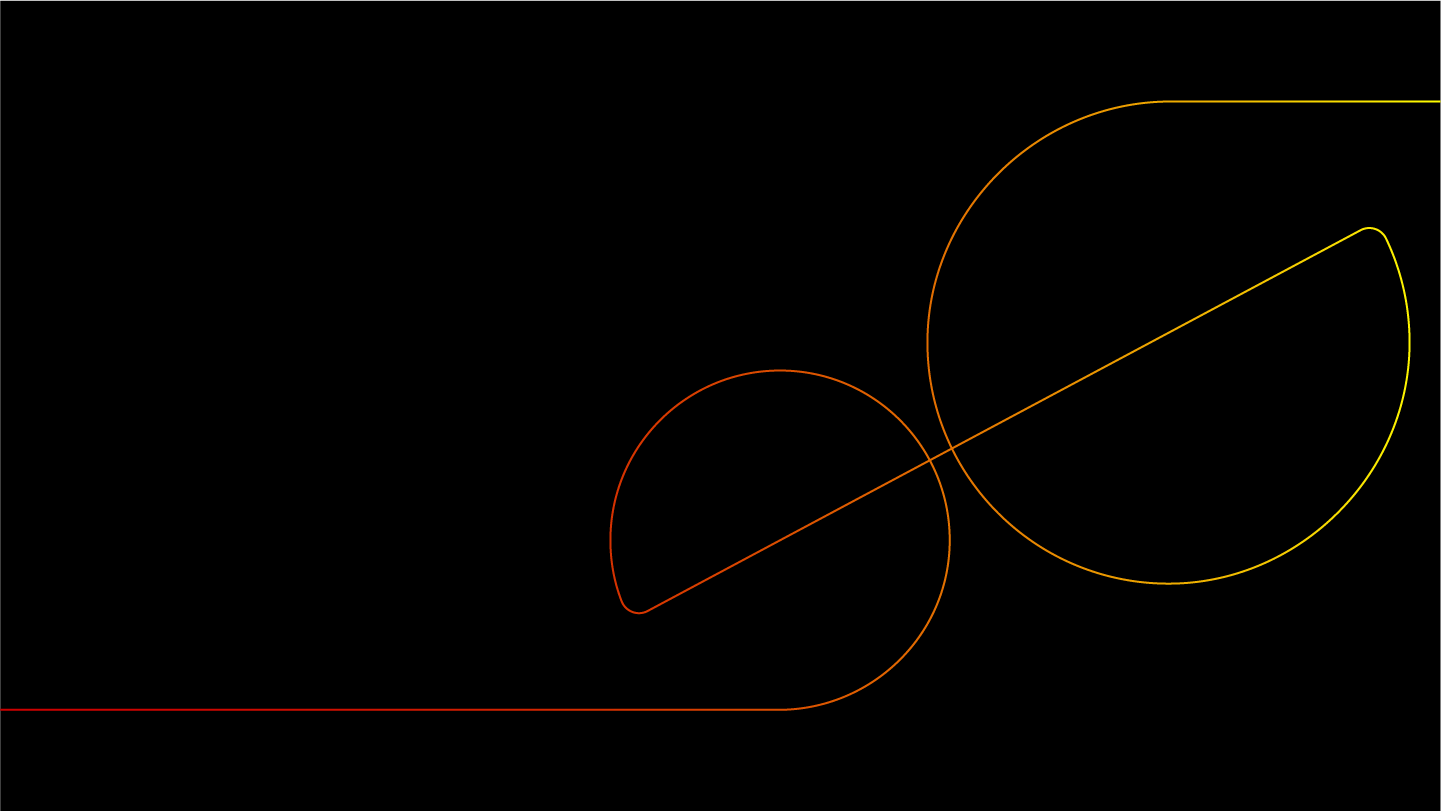
Overview
What is TPM & OEE?
Â
OEE (Overall Equipment Effectiveness) measures the productiveness of projected production time. OEE measures three types of productivity loss: Availability, Performance, and Quality.
OEE is tied to TPM goals of No Breakdowns (measured by Availability), No Small Stops or Slow Running (measured by Performance), and No Defects (measured by Quality). OEE must be measured to uncover and quantify productivity losses and to follow TPM improvements.
State of TPM
Meeting the Goal of the Total Productive Maintenance
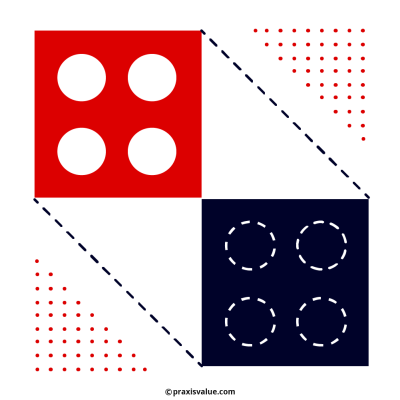
The supporting pillars of efficiency and competitiveness in the manufacturing industry are a high degree of automation, intensive networking of production and logistics, and the use of LEAN principles. These concepts are usually supported by a conscious avoidance of buffers: any failure or under-utilization of machinery and plants can disrupt the entire value-added process and jeopardize the company’s objectives.Â
As a result, the importance of effective and predictive maintenance, asset and capacity management is growing in the context of Industry 4.0 and Smart Factory. The reliability, availability, and process stability of plants and technical infrastructure, as well as low maintenance costs and great transparency of capacity usage, are critical here.Â
Total Productive Maintenance aims to meet these requirements (TPM). TPM’s guiding vision is integrated and cross-divisional asset management with the goal of continuously enhancing the productivity and quality of operational production processes. Overall equipment effectiveness is the main performance metric (OEE).
What to Expect
Improvements in all the facets of manufacturing, enhancing the effectiveness and efficiency.
Minimize production costs, expenses related to equipment stoppage & unplanned repairs.
Adequate empowerment, clarification of roles and responsibilities for workers & employees.
Delivering right quality & quantity of products to the customer at the right time effectively.
Leads to better job satisfaction and staff morale, increased throughput and product’s quality.
Uncovering underlying problems & challenges to maintain a streamlined work environment.
Our Approach
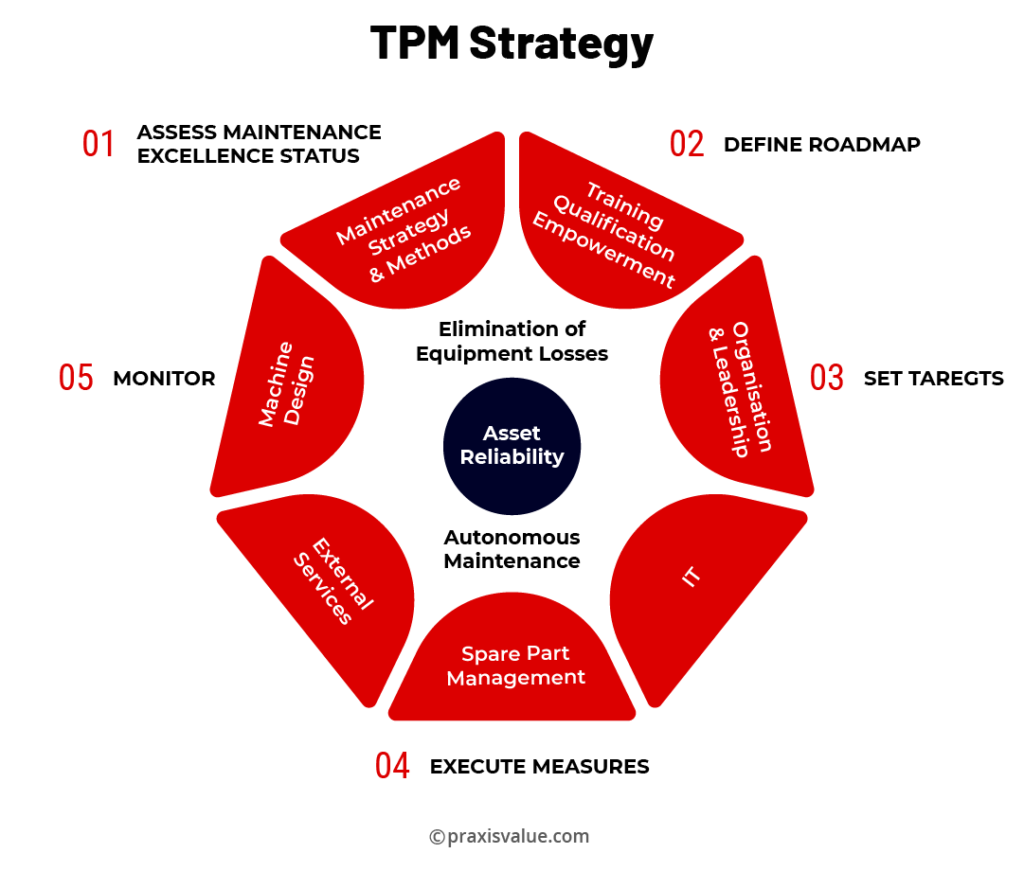
Praxis Value helps manufacturers define and implement TPM, OEE, and Maintenance Excellence. Praxis Values’ Maintenance Quick Scan begins the process. A strength-weakness profile of current performance, procedures, organization, and cost structures is produced using benchmarks and best practices from many implementation projects. On this premise, improvement potentials are defined and developed into an action target system.
The way that businesses operate and the competitive environment in which they operate are both being disrupted on a regular basis. It’s difficult to keep up, therefore your company needs to be adaptable and quick to change, with a culture that recognizes, welcomes, and even encourages business transformation. Praxis Value’s qualified specialists and industry expertise, experience, and ability to assist organizations to identify the path ahead and create a road map that will bring them there profitably and efficiently.
At Praxis Value we leverage facts to make impactful decisions, with the goal of maximizing financial value, and this spirit infuses all we do. Our approach is to capitalize on the potential opportunities, which results in an increase in EBITDA.
Benefits
Client Results - Case Study
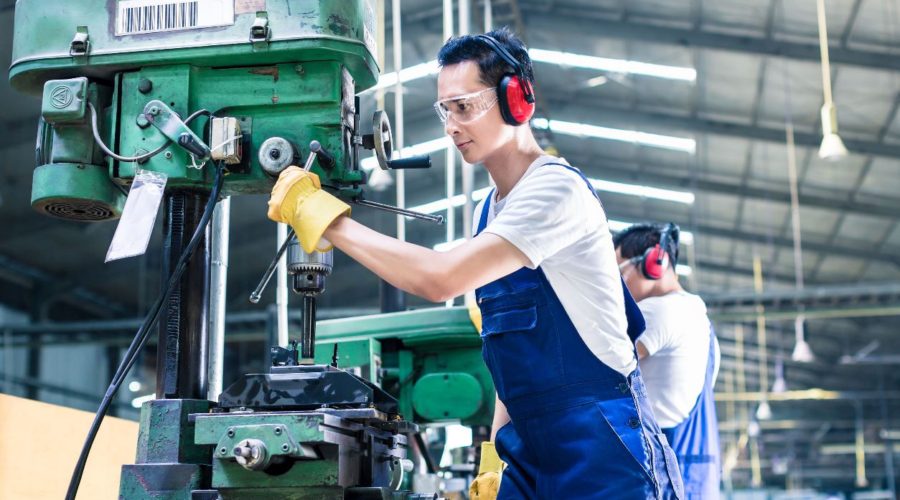
Industry – Industrial Engineering
A manufacturing was suffering from slow growth and diminished market share. To remain competitive, it needed to improve its manufacturing facilities to reduce cost and increase capacity. It also need to invest in innovation to remain competitive. Praxis Value Incorporated Lean Six Sigma principles to improve the company’s plant performance, which yielded 15 percent cost savings and increased flexibility.
Business Transformation with Praxis Value​
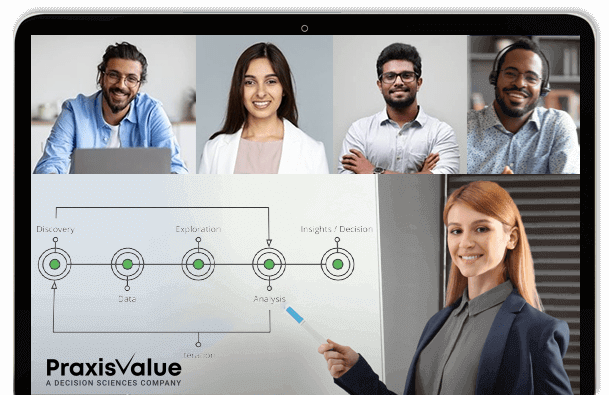
Unlocking Value Fast
By focusing on the key areas for innovation, Capabilities & performance alignment with key enterprise strategies
Sustaining Success
By collaborating with leaders across the company to ensure that operational advantages are sustained over time
Strengthening Capabilities
By offering organizations the digital tools, skills, and expertise they need to tackle the operational challenges
Optimizing the Supply Chain
By dismantling silos and establishing transparency across the operational themeRelated Services
What we think
What can we help you achieve?
You are on the way to the easiest business growth ever. Don’t hesitate and reach us today to change the future